1/4 Turn vs Multi Turn Shut Off Valves: Which is Better?
Shut off valves are essential components in plumbing and industrial piping systems. They allow you to stop or regulate the flow of liquids or gases through pipes. The two main types of shut off valves are 1/4 turn valves and multi turn valves. Both have their advantages and disadvantages depending on the application.
Choosing the right type of valve for your needs comes down to a variety of factors like flow control, size, temperature/pressure, frequency of use, and ease of operation. In this article, we’ll compare 1/4 turn vs multi turn valves, when to use each type, the pros and cons of each, and tips for installation and maintenance.
Table of Contents
Here is an in-depth comparison table for 1/4 turn vs multi turn shut off valves:
Factor | 1/4 Turn Valves | Multi Turn Valves |
Operation | 90 degree rotation to open/close | Multiple 360 degree turns to open/close |
Flow Control | Only fully open or closed | Precise throttling control |
Shut Off | Prone to leakage as seals wear | Tighter shut off when closed |
Speed | Very fast operation (seconds) | Slower due to multiple turns |
Torque | Very low torque required | High torque required |
Pressure Rating | Lower pressure ratings | Withstand very high pressures when closed |
Cost | Lower initial cost | More expensive |
Flow Path | Fully open bore when open | Higher pressure drop when open |
Status Indication | Position is visually evident | Position is not readily evident |
Temperature Rating | Up to ~400-500°F for high temp. models | Can handle very high temps >1000°F |
Valve Types | Ball, butterfly, plug valves | Gate, globe, needle valves |
Size Range | 1/4″ to 72″ diameter range | 1/8″ to 72″ diameter range |
Frequency of Use | Ideal for frequent on/off operation | Okay for infrequent operation |
Durability | Prone to wear over time | Very durable |
Applications | Steam, fuel/gas lines, water lines | Steam boilers, process control, high pressure |
Maintenance | Requires more frequent seal replacement | Requires less routine maintenance |
Price | Check Latest Price | Check Latest Price |
What are Shut Off Valves?
Definition
Shut off valves, also called isolation valves or stop valves, are devices installed in fluid piping systems to control or stop the flow. By closing the valve, you can shut off the supply of the fluid or gas to downstream piping. This allows for routine maintenance, repairs, or modifications to the system.
Purpose
The main purposes of shut off valves include:
- Stopping or regulating flow
- Isolating sections of piping
- Throttling flow
- Relieving pressure
- Preventing backflow
- Facilitating maintenance and repairs
Proper placement of shut off valves at strategic points in a piping system is crucial for operation and safety. They allow you to shut down only the section that needs work rather than the entire system.
Types
Some common types of shut off valves include:
- Ball valves – 1/4 turn valves with a ball-shaped disk to stop flow
- Butterfly valves – 1/4 turn valves with a disc to block flow
- Gate valves – multi turn valves that lift/lower a gate to obstruct flow
- Globe valves – multi turn valves that use a disk & stem to regulate flow
- Plug valves – 1/4 turn valves with a tapered or cylindrical plug to block flow
Ball, butterfly, and plug valves are quick 1/4 turn types, while gate and globe are multi turn valves.
1/4 Turn vs Multi Turn Valves
Next, let’s look at the distinction between 1/4 turn and multi turn valves and the benefits of each design.
What are 1/4 Turn Valves?
Definition
1/4 turn valves require a 90 degree turn to fully open or close the flow passage. Common 1/4 turn valve types are ball, butterfly, and plug valves. They operate from the fully open to fully closed position, or vice versa, in a 1/4 turn (90 degrees).
Benefits
- Fast operation – The 1/4 turn allows for quick isolation in emergency situations.
- Clear status indication – Their fully open or closed status is easy to determine at a glance.
- Low operating torque – They require less torque and are easier to operate than multi turn valves.
- Streamlined flow – Their bore is fully opened leading to low pressure drop.
- Compact size – Their simple mechanism allows for smaller, lightweight designs.
Use Cases
1/4 turn valves are ideal for applications requiring:
- Frequent operation
- Fast isolation in emergencies
- Low pressure loss
- Low operating torque for easy opening/closing
- Small size and weight
Common uses include steam lines, fuel/gas lines, water lines, and industrial/chemical processing pipes where you need to start/stop flow quickly.
What are Multi Turn Valves?
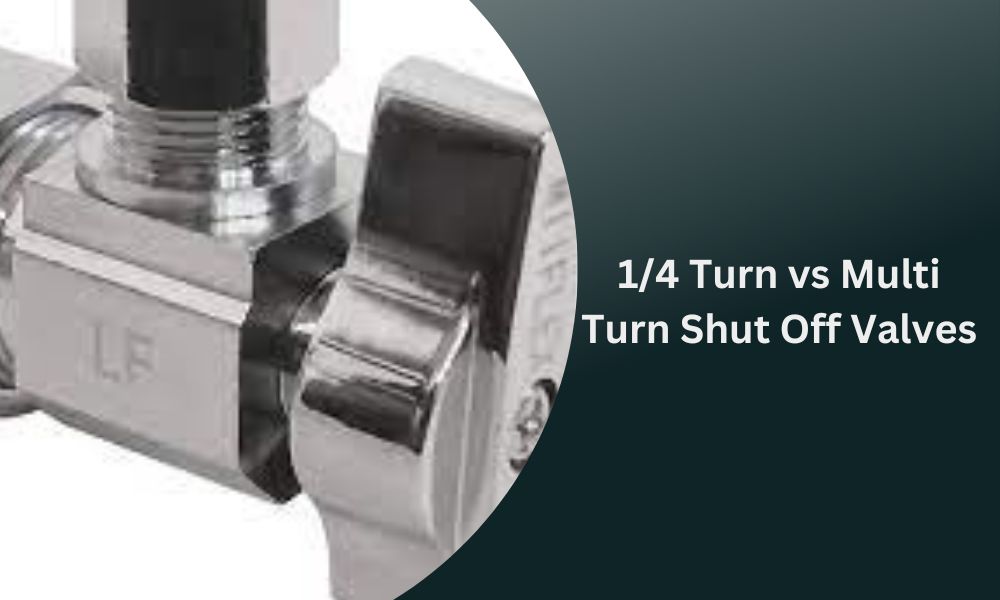
Definition
Multi turn valves require multiple 360 degree turns to open and close the flow path. The number of turns can vary from 5 turns to 20 or more turns. Gate, globe, and needle valves are common multi turn valve types.
Benefits
- Precise flow control – Their multi turn design allows for precision flow regulation.
- Tight shutoff – The extra turns enable a tight seal when closed.
- Throttling ability – They can fine tune intermediate flows between open and closed.
- High pressure rating – Can withstand very high pressures when closed.
Use Cases
Multi turn valves excel in applications that call for:
- Fine flow control rather than complete on/off operation
- Gradual opening/closing
- Higher pressure systems
- Tight shut off when closed
They are widely used in steam boilers, process control systems, high pressure hydraulic lines, metering, and throttling services.
Key Differences
To summarize the main differences:
- Operation: 1/4 turn valves open/close in a 90 degree rotation while multi turn valves require multiple 360 degree turns.
- Flow control: 1/4 turn valves offer only fully open or closed flow while multi turn valves enable precise throttling.
- Shut off: Multi turn valves provide tighter shut off when closed. 1/4 turn valves can leak unless the seals are in perfect condition.
- Speed: It takes only seconds to operate a 1/4 turn valve compared to the longer time for multiple turns of a multi turn valve.
- Torque: The torque required to operate a 1/4 turn valve is much lower than a multi turn valve.
- Pressure rating: Multi turn valves generally have higher pressure ratings when closed than 1/4 turn valves.
- Cost: Multi turn valves are typically more expensive than 1/4 turn valves of the same size and materials.
When to Use Each Type
Next we’ll go over some of the factors to weigh when choosing between 1/4 turn vs multi turn valves for an application.
Factors to Consider
Flow Control
If you simply need to fully open or close a flow path, a 1/4 turn valve is the choice. For precision throttling, opt for a multi turn valve.
Size
For larger piping systems, multi turn valves might become impractical for operation. Their increased torque makes them hard to open/close. 1/4 turn valves are better suited for large diameter pipes.
Temperature/Pressure
Multi turn gate valves are better built to withstand very high pressures and temperatures vs. most 1/4 turn valves. Choose multi turn valves if your system exceeds the pressure/temperature limits of 1/4 turn models.
Frequency of Use
If you’ll be operating the valve very frequently, the fast 1/4 turn action is preferable over taking multiple turns each time. Multi turn valves are fine for infrequent operation.
Recommendations
As a general rule of thumb:
- For on/off applications, use a 1/4 turn ball, butterfly, or plug valve.
- For throttling, precision flow control, or high pressure needs, use a multi turn gate or globe valve.
- For corrosive fluids, use a ball or butterfly valve with corrosion resistant materials.
- For very large piping, opt for a butterfly or ball valve over multi turn gate.
- For high temperature steam or gases, choose a multi turn gate valve rated for the temperature.
- For frequent operation, the ease of 1/4 turn valves is beneficial.
- For hazardous fluids, multi turn valves provide tighter shutoff when closed.
Pros and Cons of Each
Now let’s examine the specific benefits and drawbacks of both valve types.
1/4 Turn Valve Pros and Cons
Pros
- Fast open/close operation
- Low operating torque
- Clear status indication
- Streamlined flow when open
- Compact and lightweight
- Lower initial cost
Cons
- Limited flow control between open and closed
- More prone to leakage over time as seals wear
- Lower pressure ratings in general
- Not suitable for throttling applications
- Tendency to slam open/closed if operated too quickly
Multi Turn Valve Pros and Cons
Pros
- Enable precise flow control and throttling
- Provide tight shut off when closed
- Withstand very high pressures when closed
- Gradual opening/closing action
- Tight sealing for hazardous fluids
- Can use with high temperature fluids
Cons
- Slow to operate with multiple turns to open/close
- Require greater torque to operate
- More expensive than 1/4 turn valves
- Not practical for large diameter pipes
- Higher pressure drop when open
Installation and Maintenance
Proper installation and maintenance is key to getting the best performance and longevity from your shut off valves. Here are some important tips.
Installation Tips
- Ensure adequate space around the valve for operation and servicing.
- Install vertically upright if possible to prevent sediment buildup inside the valve.
- Allow some slack in adjacent piping for thermal expansion and contraction.
- Use valve sizes matched to the pipe size. Don’t undersize the valve diameter.
- Pay attention to flow direction markings on the valve body.
Maintaining Valves
- Periodically cycle the valve from fully open to closed to prevent sticking.
- Lubricate any grease fittings per manufacturer instructions.
- Check for corrosion buildup and recondition as needed.
- Replace worn out gaskets, seals, and washers.
- Verify bolts and connections are properly tightened.
Extending Valve Lifespan
- Never force a stuck valve open or closed. Disassemble and service first.
- Replace worn parts like balls, seats, and stems to prevent leaks.
- Keep accurate records of maintenance performed.
- Ensure proper system pressure, flow rate, and temperature.
- Isolate and insulate valves from excessive vibration or shock loads.
FAQs
What is the benefit of a 1/4 turn valve?
The main benefits of 1/4 turn valves are fast on/off operation, low operating torque, clear status indication, streamlined flow when open, compact and lightweight design, and lower cost compared to multi-turn valves.
When should I choose a multi turn valve instead of a 1/4 turn valve?
Multi turn valves are preferable when you need precise throttling control rather than just on/off operation, ability to withstand very high pressures, tight shut off for hazardous fluids, suitability for high temperatures, or frequent operation where the multiple turns are not inconvenient.
What are the most common types of 1/4 turn valves?
The most common 1/4 turn valve types are ball valves, butterfly valves, and plug valves. All provide quick open/close operation in a 90 degree rotation.
How many turns does it take to operate a multi turn valve?
Multi turn valves require multiple 360 degree rotations to go from fully open to fully closed. The number of turns can range from 5 turns to 20 or more turns depending on the valve type and size.
When should I use a ball valve versus a gate valve?
Use a ball valve for on/off applications where you need quick operation. Use a gate valve when you need to precisely throttle flow or require a valve that can withstand very high pressures when closed. Ball valves are also preferred for larger pipe sizes.
Conclusion
In summary, 1/4 turn and multi turn valves both offer distinct advantages depending on the needs of the application. 1/4 turn valves shine for frequent on/off usage, fast isolation, low pressure loss, and easy operation. Multi turn valves are designed for precision flow throttling, high pressures, and tight shut off.
Consider the service, flow control requirements, operating frequency, and system conditions when selecting between these two valve types. Proper installation and maintenance will also ensure you get optimal performance and life from your valves. Understanding the pros and cons of each style will allow you to make the smartest choice.